Lubricant Testing 101 (ASTM Oil Tests)
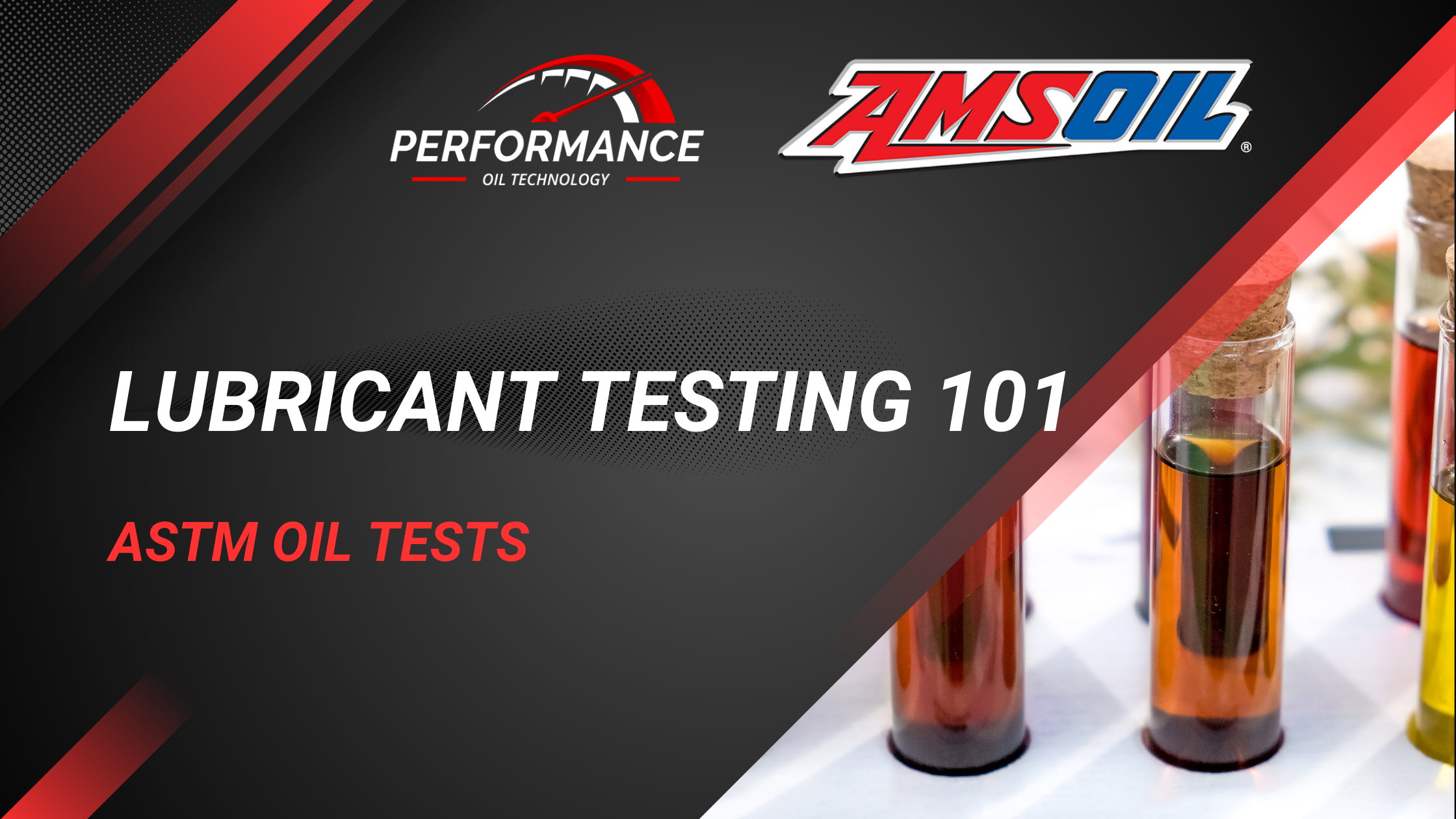
Top Insights
Many chemical, physical, and performance tests exist for motor oils and other automotive lubricants. I will cover the most commonly used ASTM tests. The ASTM is the American Society for Testing and Materials. It is a scientific, engineering, and technical organization that develops standards on the performance parameters and physical characteristics of specific materials used in engineering and manufacturing.
Pour Point (ASTM D-97)
What is an oil's pour point?
An oil's pour point is the lowest temperature at which the oil will flow. Most petroleum-based oils have waxes and paraffin that solidify at cold temperatures. Oils with more waxes and paraffins will have a higher pour point, while highly refined and synthetic oils will have significantly lower pour points. The viscosity of an oil also affects the pour point. Even though it may be wax and paraffin-free, an oil with a high viscosity is still limited in its pour point due to the higher viscosity.
The pour point is a critical parameter, especially for people in cold climates. The oil must be able to flow into the oil pump and be pumped to various parts of the engine at the lowest anticipated temperatures. The pour point should not be the only selection criteria for cold weather operations, however. The fact that a motor oil has a specific pour point does not necessarily mean that it will adequately pump through the engine at the lowest pour point temperature for which the oil is rated. A low pour point combined with the frictional effect of the oil being pumped through a vane or rotor-type oil pump and heat from the engine gradually warming the oil will cause the oil flow to increase so that it properly flows to the necessary engine components.
Additionally, the pour point of motor oil can change with time in service as the pour point depressant additives in petroleum-based oils are consumed. Synthetic motor oils do not use these pour point depressants and thus have much more consistent pour points after time in service.
Flash Point and Fire Point (ASTM D-92)
What is an oil's Flash Point?
The flash point is the lowest temperature at which a flame will cause the vapors of a lubricant to ignite.
What is an oil's Fire Point?
The fire point is the lowest temperature at which a particular oil will sustain burning for five seconds. The test sample is heated, and a flame is brought near its surface.
Flash point tests are the most commonly used flammability tests and are typically used for safety of shipping, handling and storage of lubricants. Generally, in specific high-temperature engine operations, oil with a low flash point would indicate higher volatility and thus may result in higher oil consumption rates.
Both flash and fire points can be drastically reduced when fuel contamination is present in motor oil.
SAE Viscosity Grade
An oil's viscosity (thickness) is typically it's first line of defense in minimizing wear. Oils, like all fluids, are non-compressible by nature and when placed between two moving components, will keep the components from contacting one another. However, there is a point at which the oil film separating the two components is insufficient and contact occurs.
The point at which this contact occurs is a function of an oil's viscosity. Typically, the more viscous or thicker the oil, the greater the load it will carry.
Common sense suggests the more viscous the oil is superior. However, higher viscosities also present unique disadvantages like being more difficult to circulate, especially at colder temps.
The Society of Automotive Engineers (SAE) made fluid viscometrics easier to understand for consumers by developing a grading system based on an oil's viscosity at specific temperatures.
Equipment manufacturers decide the most appropriate viscosity for an application and indicates which SAE grade is most suitable for a particular piece of equipment.
For example, for a 5W-30 grade oil, the "5W-30" denotes the oil's viscosity at cold temperatures (W standing for Winter) and the "30" represents the oil's viscosity at normal operating temperatures.
Kinematic Viscosity (ASTM D-445)
What is an oil's Kinematic Viscosity?
Kinematic viscosity measures the time it takes for a known volume of oil to flow under gravity through a calibrated glass capillary viscometer. To have standard reporting temperatures, kinematic viscosity is measured at 40 degrees C. (104 deg. F) and 100 deg. C. (212 degrees F.). It is essentially the ratio of the viscosity to the density of the oil being tested.
Kinematic viscosity is typically measured in centistokes (cSt). Centistokes can be thought of as the result of dividing the dynamic viscosity of an oil by its density, both measured at the same temperature.
Dynamic viscosity (measured in centipoise or Pascal seconds) is the force required to overcome fluid friction in an oil film of known dimensions and thickness. I will not go into detailed engineering descriptions and calculations of dynamic viscosity as it gets into complex engineering calculations. I will explain kinematic viscosity in relation to practical applications in selecting a multi-viscosity 30-weight motor oil in another article.
Viscosity Index (ASTM D-2270)
The viscosity index determines how much a particular motor oil's viscosity changes with temperature. It is a method of applying a number to this rate of change based on a comparison with two arbitrarily selected oils (published in tables by the ASTM at a given temperature, typically 40 deg. C and 100 deg. C) that have significant variations in viscosity index.
A high viscosity index would indicate a low rate of change of viscosity with temperature, while a low viscosity index would indicate a high rate of change of viscosity with temperature. High viscosity index motor oils protect engines that operate with temperature variations better, including all auto and light truck engines. Motor oils with a large amount of viscosity index improvers tend to degrade more rapidly than those with less viscosity improvers.
By their inherent nature, synthetic oils have significantly fewer viscosity improvers than equivalent viscosity in petroleum oil and thus tend to have high viscosity index values and are more stable.
Although higher viscosity index ratings are more desirable, it doesn't accurately represent that oil's high temperature viscosity or it's load carrying ability. Shearing forces within the engine (and particularly transmissions) can significantly reduce an oil's viscosity.
Therefore, oils with a lower viscosity index but higher shear stability can actually have higher viscosities at operating temperature than one with a higher viscosity index and lower shear stability.
High-Temperature/High-Shear Viscosity (ASTM D-5481)
This is a severe service test that measures the viscosity under high temperatures and high shear rates and is measured in units of centipoise. Lubricants with high values in this test will maintain their viscosity in high engine operating temperatures and when exposed to high load/high shear conditions.
Ultimately this test combines viscosity, shear stability, and viscosity index. During high temperature operations bearings require the greatest level of protection.
NOACK Volatility (ASTM D-5800)
This test is used to determine the evaporative losses of motor oil at high temperatures. Motor oils with high evaporative losses will have higher oil consumption rates. In addition, motor oil that has higher evaporative losses in high-temperature operation will have increased lacquer and varnish deposits as well as other negative changes in the particular oil's chemical properties.
A lower NOACK volatility rating indicates a motor oil that will have less evaporative losses and thus less oil consumption and increased engine protection and resistance to varnish, lacquer, and sludge formation in critical engine areas such as pistons, cylinders, and valvetrain components.
Four-Ball Wear Test (ASTM D-4172B)
The Four-Ball Wear Test is one of the most widely known and used tests for measuring the wear-preventative characteristics of lubricating oil. The machine consists of three fixed steel balls and one rotating steel ball. The machine can be set to different speeds, loads, and temperatures. The balls are put into a bath of the particular oil being tested, and the test is typically run for one hour at a specific load and RPM. At the completion of the test, the average wear scars on the three fixed balls are measured and reported.
Although this test does not simulate any bearing geometry internal to an engine, it is extremely useful in comparing the wear protection properties of various lubricants. Since the only variable in the test is the particular brand of oil, it provides an accurate comparison as to how well a lubricant will prevent wear inside an engine when compared to another competitive brand of oil of the same viscosity. In other words, it is an "apples to apples" test comparison. The smaller the wear scar, the better the protection.
AMSOIL is one of the only manufacturers that I am aware of that prominently displays and advertises how their oils perform in this test. AMSOIL shows independent laboratory wear scar test results of their oil on every specification sheet and on the bottles of two of their high-performance oils. I have yet to see another manufacturer that does well enough in these tests to display the results. I have contacted many other oil manufacturers and am told that they do not advertise or disclose this specification to the general public.
Cold Cranking Simulator (CCS) Apparent Viscosity (ASTM- D-2602)
Viscosities that are reported using the kinematic viscosity glass capillary test method do not adequately represent how motor oil performs under cold cranking conditions. Therefore, the Cold Cranking Simulator (CCS) test was developed to predict the cold cranking properties of oils used in automotive and truck crank cases. A 5 ml sample of oil is placed in the shear zone of the CCS test machine at room temperature. The shear zone consists of a rotor and stator. The coolant then begins to flow in order to drop the temperature of the oil. After three minutes, the engine is run for one minute before the machine's rotor speed is read.
The CCS viscosity is determined in centipoises (cP) by referencing the speed readings obtained with a special calibration curve determined by standard reference oils. The resultant viscosity is called the apparent viscosity at low temperatures. This test is extremely useful in predicting engine-cranking viscosities at specified low temperatures and how easily an engine will start in cold temperatures.
Borderline Pumping Temperature (ASTM D-3829)
The borderline pumping temperature is the lowest temperature at which a particular motor oil can be continuously and adequately supplied to the critical components of an internal combustion engine. In order to start an engine in cold temperatures, certain minimum cranking speeds are required. If motor oil exists with a viscosity that is so high that the engine is not capable of turning over fast enough, it will not start. This is the primary reason oil and automotive manufacturers specify specific oil grades in specific ambient temperatures and batteries with adequate Cold Cranking Amperage (CCA).
In general, gasoline engines do not require as high of cranking speeds as diesel engines. The colder it gets outside, the higher cranking speeds are required of diesel engines. Diesel engines operate on the principle of adequate compression temperature sufficient to start the combustion process, which in turn depends on the ambient temperature and the cranking speed. This is why diesel engines use higher capacity, higher amperage dual batteries, and heated intake air or heated crankcases and fuel tanks. Synthetic motor oils drastically improve the stability of both gasoline and diesel engines at low temperatures.
Recently, I had a situation where a company I was consulting on their equipment was having cold starting problems with their heavy diesel logging and excavating equipment in the extremely cold winter temperatures of northern Michigan. The equipment was left outside, away from any source of electricity, so that block heaters could not be used. Often, before starting the equipment, special propane-powered heaters had to be aimed at the oil pan and engine block in order to sufficiently warm the engine and allow it to turn over at a high enough RPM to start the combustion process.
After I recommended that they change to synthetic diesel oil, the company no longer had starting problems. The oil I recommended has a pour point of minus 44 deg. F and CCS viscosity of 2120 at minus 5 deg. F. Synthetic oils do not have the waxes and paraffins that petroleum oils do and have drastically improved cold weather pumping and flow characteristics.
Total Base Number (TBN) (ASTM D-2896)
The Total Base Number (TBN) is a measure of the reserve alkalinity of motor oil and how well the oil can neutralize harmful acidic by-products of combustion. The detergent/dispersant additive package is critical in determining how effective the motor oil is in neutralizing these acids. TBN depletes with time in service. Higher TBN oils are more effective at neutralizing acids for longer periods of time. In engine lubrication systems that use by-special pass filtration systems and do not change oil, TBN is monitored through oil analysis testing and also maintained by replenishing oil added during filter changes and topping off the oil.
A more specific explanation of TBN and TAN is as follows and is repeated as specified by Exxon Mobil. It is very important that you understand TBN: TBN is the quantity of acid, expressed in terms of the equivalent number of milligrams of potassium hydroxide, that is required to neutralize all basic constituents present in one gram of oil. This test is normally used with oils that contain alkaline, acid-neutralizing additives. The rate of consumption of these additives (TBN depletion) is an indication of the projected serviceable life of the oil. With used oils, it indicates how much acid-neutralizing additive remains in the oil. Typical oils of this nature include diesel engine oils for internal combustion engines that use fuels containing acid-producing constituents such as sulfur or chlorine. As long as any significant amount of TBN remains in the oil, there should not be any strong acids present. However, the nature of high alkaline and metallic antioxidant additives sometimes allows for both TBN and TAN values to be obtained on the same sample. This occurs for both new and used oil (z).
Total Acid Number (ASTM D-664)
The Total Acid Number (TAN) of an oil is the weight in milligrams of potassium hydroxide required to neutralize one gram of oil and is a measure of all the materials in an oil that will react with the potassium hydroxide under specified test conditions. The usual major components of such materials are organic acids, soaps of heavy metals, intermediate and advanced oxidation products, organic nitrates, nitro compounds, and other compounds that may be present as additives. It is worth mentioning that new and used oil can exhibit both TAN and TBN values.
Organic acids may form as a result of the progressive oxidation of the oil, and the heavy metal soaps result from the reaction of these acids with metals. Mineral acids (i.e., strong inorganic acids), if present in an oil sample, are neutralized by potassium hydroxide and would, therefore, affect the TAN determination. However, such acids are seldom present except in internal combustion engines using high-sulfur fuels or in cases of contamination. Since a variety of degradation products contribute to the TAN value, and since the organic acids present vary widely in corrosive properties, the test cannot be used to predict the corrosiveness of an oil under service conditions (z).
Foam Tests (ASTM D-892)
In this first phase of the foam measurement test, air is blown through a sample of oil that is maintained at a specific temperature for a specific period of time. When the air supply is shut off, the foam volume is measured. This is called the foaming tendency. In the second phase of the test, the foam is allowed to dissipate for ten minutes, and then the volume of foam is measured and reported as the foam stability. The foam tendency and foam stability can change with time in service. New oils will have a lower tendency to foam and lower foam stability values, while oils that are contaminated can have increased values. The additive package in a particular oil is critical in the oil's ability to reduce/eliminate foam both when the oil is new and after an extended time in service. Certain manufacturer's oils have highly effective anti-foaming additive packages and should be considered in applications where foaming is of critical importance.
Note that all oils will foam to a certain extent when agitated. However, excessive foaming can lead to problems such as starvation at the oil pump inlet or foam being drawn into the oil pump inlet with the oil. Foam is also detrimental to hydraulic valve lifter operation and the degree of oil film protection afforded by the oil. Certain motor oils, such as motor oils intended specifically for small high RPM engines, typically have a special defoamant blended into the oil formulation. It is also important to note that excessively overfilling an engine crankcase can cause oil foaming, even with defoamants.
Get FREE Shipping!
Save up to 25% on all AMSOIL products and get FREE shipping on orders of at least $100. Learn more below.
Related Articles
SAVE 25% + FREE Shipping!
Sign up today for 25% off all AMSOIL products and get FREE shipping on orders of $100 or more as a preferred customer.